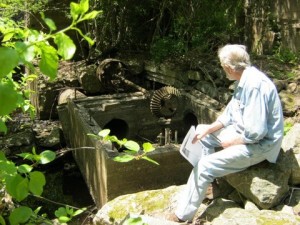
Carl Close of Middleton looks back at the ruins of the Curtis sawmill on Boston Brook where he worked as boy. It may have been at Arthur Curtis’ blacksmith shop that he was first forged into the craftsman and artist he became. The mill and Arthur’s forge are long gone. Carl’s still burns. – Middleton Stream Team photo
IRON AND WATER
Remarkable Carl Close of Middleton takes us back to an ancient art once common. Even more remarkably his son, Carl, Jr., followed suit and became a professional blacksmith. For his father it has been a lifelong hobby.
Old Stream Teamers and Closeteers like to visit Carl. He always has something new and well made to show us. It might be a resurrected horse drawn plow, a rebuilt Spanish American War cavalry rifle, a nicely refinished eighty year old gear for the Curtis Mill commemorative project, real working steam engines made from scratch, a metal sculpture, and homemade tools of all kinds, something new almost every visit.
The other day after a snowstorm when an old Closeteer visited, Carl asked him, “Want to see my new forge fan?” He likes to show his creations as much as we like to see them. At his homemade forge in a shed he also made, he added a few dry hardwood shavings and lit them. Charcoal from his house wood stove was added. Charcoal is a favored fuel of blacksmiths. A switch was flicked and the fan blew the burning charcoal red, then white hot. In no time the temperature in the center of the tiny fire was up to an estimated 2000 degrees. The blacksmith asked, “Want to try it?” and picked up a foot long piece of iron rod from the ground and passed it to his visitor. When its end was heated cherry red, the Closeteer pounded it somewhat flat as instructed and then after further heating hammered it around the horn of the anvil. Viola! Under Carl’s tutelage a round loop handle was made on one end. There was no bucket of water handy to temper, none was needed. The maker thrust the hot handle into new snow. The Closeteer was reminded of Frost’s poem “Fire and Ice”. Then the blacksmith patiently had his 80 year old pupil, who was undergoing his first forging experience, make a point for a poker at the other end from the handle. Soon the tool was finished. The novice could readily see the attraction of this once common and important trade. For Carl and son it is an art. Their palette is made up of various kinds of iron.1 Their brushes are dozens of shaping tools, hammers, and flames of various colors which they through experience can interpret.
Carl’s mentor was the late Arthur Curtis, jack of all trades and master of several.2 Arthur had a forge at which Carl helped as a boy. He probably pumped the bellows to fan the fire and did some of the heavy pounding. Inspired, at 14 he bought a small forge via a Sears Roebuck catalog, probably the most widely read book in America when we were boys. This forge was the first of others in a lifetime of shaping iron into useful and handsome things.
What has all this to do with water, our weekly subject, besides tempering already mentioned? We’ll go back to the history of iron making in our Yankee towns when low grade iron ore was extracted from bogs.3 On average about 5 % of soil is iron. When you view almost any excavation from a two foot shovel dug hole to a septic system perc test pit you’ll see just below the dark topsoil a yellowish to reddish layer of soil called by soil folks the B horizon. Most are usually rust colored. Insoluble ferric oxide is rust. Certain bacteria4 in places without enough needed oxygen for respiration have enzymes that breakdown ferric oxide to soluble ferrous oxide releasing oxygen which the bacteria use. This soluble ferrous form moves through the ground water and seeps out in low places. When it hits the air the reaction is reversed and insoluble ferric oxide is formed. This is the rusty, often slimy, water we see on the edges of swamps, bogs, and other slow moving bodies of water. The bacterial reactions sometimes smell like sewage due to a byproduct hydrogen sulfide. Another common sign besides rust in murky waters are iridescent oil slicks on the surface. One old Closeteer who roams around such places throughout Middleton often see these signs. Where the iron seeps forth year after year, iron rich layers form. This is the bog iron ore that was so important in our history from the arrival of the Old Worlders to the discovery of richer, deeper, iron deposits in the 19th century. Middleton had a bog iron works off Mill Street on Mill Pond in the 18th century.5 Water power was used to run a large trip hammer, which literally beat the iron out of heated ore and separated it from most impurities, the slag. The hot iron masses called blooms were hammered into rods and sold to area blacksmiths for use as wrought iron. Boxford also had an iron works as did Saugus in the 17th century. The latter operated only 22 years up until nearby bog iron ore deposits ran out. Saugus’ remains were found last century and a museum was built to explain this essential industry back to when iron shipped from Europe was very expensive. Middleton’s mill, its sluiceway still clearly seen, lasted much longer, but not even a bronze or stone sign marks the site.
Lura Woodside Watkins so often mentioned in the Closet has more than made up for the lack of a marker. How very lucky Middleton was to have her as a historian who wrote honestly and well about what people did for a living. She devotes two chapters to iron occupations. Chapter IV is about the Iron Works; chapter V is devoted to blacksmiths so important to all our towns, 1630s to 1920s.6 Assembly line production in factories with machines wiped out the art except for people like Carl and son.
For 300 years here, water tempered hot iron, turned mill wheels hooked to trip hammers, and shipped product to our ports for the ship smiths. In our swamps around town bog iron ore is still being quietly made by bacteria.
1 The more widely used word for metals mostly of the element iron (Fe) with small amounts of carbon (C) is steel. There are many kinds giving the mixes strikingly different properties. The science of metallurgy is beyond our purpose here so we use the word iron.
2 Brothers, the late Arthur and Earnest Curtis, were farmers on Peabody Street. They also built and ran a water powered sawmill on Boston Brook from the 1930s to 1972. Arthur a master craftsman had a woodshop and a blacksmith shop. He liked to use old tools many of his own making as does Carl.
3 Carl loaned us a book we like entitled The Blacksmith by Aldren A. Watson. It is about the basics of the art with many fine illustrations by the author.
4 Soil bacteria known to feed on iron compounds are Thiobacillus ferrooxidans and Leptospirillum ferrooxidans. There are probably other species.
5 The “Iron Works” operated from about 1708 to 1780. In the latter half of the 19th century a knife factory at the site used the water power to run machines to make special knives for shoemakers. The dam, sluiceway, and “Mill Pond” are still in fair shape. Proceed along Mill Street until you see the Emerson Brook sign.
6 Watkins, Lura Woodside. Middleton, Massachusetts: A Cultural History (Essex Institute, Salem Massachusetts) 1970
WATER RESOURCE AND CONSERVATION INFORMATION
FOR MIDDLETON, BOXFORD AND TOPSFIELD
Precipitation Data* for Month of: | Nov | Dec | Jan | Feb | |
30 Year Normal (1981 – 2010) Inches | 4.55 | 4.12 | 3.40 | 3.25 | |
2013 – 14 Central Watershed Actual | 3.35 | 5.30 | 3.47 | 3.10 as of 2/25** |
Ipswich R. Flow Rate (S. Middleton USGS Gage) in Cubic Feet/ Second (CFS): For Feb 25, 2014: Normal . . . 85 CFS Current Rate . . . 79 CFS
—————————————————————————-
*Danvers Water Filtration Plant, Lake Street, Middleton is the source for actual precipitation data thru Jan. Normals data is from the National Climatic Data Center.
**Updated Feb precipitation data is from MST gage.
THE WATER CLOSET is provided by the Middleton Stream Team: www.middletonstreamteam.org or <MSTMiddletonMA@gmail.com> or (978) 777-4584